High-tech manufacture
More and more automobile manufactures are using floor transport systems with CPS
The range of applications of the "Contactless Power System" (CPS)
from VAHLE grows constantly. After a CPS pilot system was installed on a container crane in the USA
in the summer of 1997, the automobile industry has been using this technology of the future
from Kamen.
In the autumn of 1998, one of the European automobile manufacturers started to use
the CPS technology from VAHLE. For the first time a production line was equipped with
a floor transport system using a contactless power supply. The traditional conductor
systems which had been used before functioned reliably; however, they required
frequent maintenance. Therefore, it was time for CPS. It is used for the assembly
of the car chassis and the gearbox/engine unit. Because of the system's completely
contactless mode of operation, maintenance is reduced to a minimum. This is a
decisive factor, since this can considerably increase the availability and lifetime of the
transportation system.
37 vehicles simultaneously
The floor transport system for the assembly of the chassis consists of a 174 m
long line with three switches and two lifting stations. The chassis joins the car body
at the lifting stations. A total of 22 carriers are in use on this line. The
approx. 120 m long floor transportation system for the assembly of the gearbox/engine
units including one switch is equipped with a total of 37 carriers.
The CPS system transfers the power to the two assembly lines using the principle
of induction, similar to that of a conventional transformer in which the primary
and the secondary winding are on a closed ferromagnetic core, in the CPS system
the stationary primary winding is straightened to a long conductive loop. The mobile
secondary winding (pick-up coil) is placed on an open ferromagnetic core and coupled
with the magnetic field of the primary winding. This enables the two windings to move
freely relative to each other.
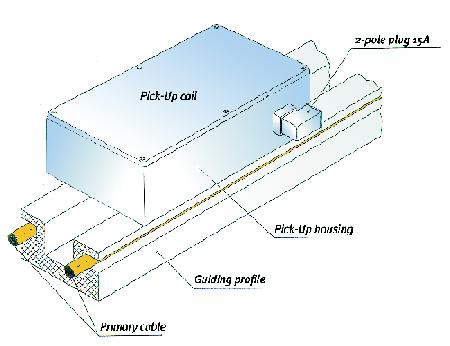
Optimum power transmission
An optimum and low-loss power transmission is provided by the CPS primary inverter which transforms the 50 Hz A.C.
main voltage into a single-phase 20 kHz voltage and then feeds it to the CPS
primary conductor. Each assembly line has a central 45 kVA feed terminal. The
primary inverter was generously dimensioned for the given number and the power range of
the carriers and it even allows for a further expansion of the line with extra carriers.
For optional reasons, the customers demanded that selected sections of the
installation where to be switched off. This requirement was met by technical
alterations of the CPS system. The primary cable is installed underfloor in a
guide profile specially designed for this application. The external groove in
the plastic profile is of no significance for the CPS system; only serves to guide
the carrier with a guiding roller mounted to its running gear.
What happens when the carriers come close to the switches and lifting stations?
Here the primary cable is interrupted and fed separately. The dead area between
the sections is reliably bridged by a special design of the pick-up elements.
The flat shape of the pick-ups allows a space-saving mounting under the carrier.
The ideal gap between the pick-up unit and the surface of the guide rail is 15 mm.
This distance allows large movement tolerances of the carrier and guarantees a
reliable power transmission under all operating conditions.
CPS - the right path
The great interest of the industry in this innovative technology shows that VAHLE was on the right
track when deciding to develop and market the CPS system. VAHLE is convinced that
the CPS technology, due to its advantages over conventional systems, will prevail
on the market soon
Oktober 1999